‘Lafarge Zim engages Govt on cost’
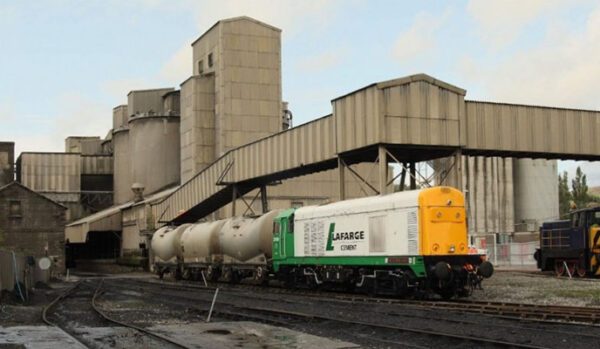
Lafarge Cement Zimbabwe is seeking Government intervention in reducing key cost-drivers that are making its products uncompetitive compared to its regional peers.
The group has taken note of efforts such as macro-economic stabilisation through the introduction of the Reserve Bank of Zimbabwe’s foreign currency auction system, but management said there are still factors that are driving up costs for local manufacturers.
For Lafarge, electricity and distribution costs are currently very high.
“We continue to engage government on a number of cost drivers that will make our industry more competitive such as cost of power (electricity and coal): Cement production is one of the most energy intensive processes consuming an average of 4 to 5 Gigajoules per tonne, which represents 20 percent to 30 percent of total production costs,” said Lafarge Zimbabwe CEO Precious Nyika.
“Just to give a comparison, the coal price ex-factory is about US$42 per tonne in Zimbabwe, compared to US$30 per tonne in South Africa and Botswana.
“Another major cost driver is distribution. Regional players have benefited from the use of railway systems. As an industry, we envisage we will be able to do the same more frequently. Today, rail cost in Zimbabwe is 7,00 US cents/km/tonne vs 1,79 US cents/km/tonne for
South Africa and 3,92 US cents/km/tonne for Zambia. Road transportation in Zimbabwe delivers cement at 11US cents/km/tonne vs 7 US cents/km/tonne for South Africa.
“We thank Government as engagements around such issues always bear results and ensure the ease of doing business. The Forex Auction System and the introduction of SI-89 of 2021 are a clear testimony of this result-oriented governance,” she added.
Notwithstanding the present challenges the group said it remains focused on expansion, as indicated by its new US$2,8 million dry mortars (DMO) plant launched this week.
The DMO project is part of Lafarge-Holcim Group’s wider US$25 million additional investment of its Zimbabwean subsidiary.
Said Lafarge Zimbabwe chairman Kumbirayi Katsande: “Lafarge Zimbabwe has not been operating in the safe survival mode, but rather we are vying for growth. We are not intimidated by the uncertainties and difficulties which business is facing to one degree or another. We cannot wait for everything to be perfect.”
Lafarge expects 3D printer in Q3
Meanwhile, the group says it expects to bring in its game-changing 3D printing technology in the third quarter of this year.
Zimbabwe is one of three countries on the continent (along with Malawi and Kenya) where the Lafarge-Holcim is pioneering the technology.
14Trees, a Lafarge Holcim joint venture with CDC Group, a United Kingdom-based investor, is deploying 3D printing technology at scale to build affordable and low-carbon housing and schools in Africa.
“We anticipate that we will receive the printer in the third quarter through a subsidiary of Lafarge-Holcim called 14Trees and we look forward to the usual Government support in its importation and subsequent approval for use,” said the CEO.
This week, the cement producer launched a new US$2,8 million dry mortar mix plant that will be producing the required 3D printing ink for local projects.
3D printing is the moulding of a structure by precisely placing volumes of material in sequential layers on top of each other, constructing from the ground up.
The material is pushed through a nozzle which regulates flow and is guided by computer-controlled positioning process. The material used in the process is cement based with sand and specially designed admixtures as additives.
“Lafarge remains committed to supporting the national housing development agenda through the introduction of new, exciting, game changing technology to address some of the challenges with traditional methods of construction – 3D printing.
“The benefits include increased construction speed; up to 70 percent faster than conventional method, enhanced sustainability as less materials are used (50mm thick walls versus 140mm) and affordability as construction costs are estimated to come down as much as 20 percent,” she said.
To showcase the capabilities of 3D printing, Lafarge Zimbabwe will construct 10 units in Knockmalloch under the affordable housing project that is currently underway.
“This project will afford relevant stakeholders to witness and experience the capabilities of this and innovative technology and it is anticipated that this will attract more projects towards the use of the technology to provide decent affordable housing starting in Malawi,” added Nyika.
“With its high speed of construction and optimised material use, this technology reduces the carbon footprint for building new homes by up to 70 percent.”
Business Weekly