Training miners for real-life blasting experiences often involves taking workers up to 3,000 feet underground, and actual training can be tedious, costly, and dangerous.
In a recent case study, Anglo American began implementing motion capture technology at some of its platinum mines in South Africa, where they paired virtual reality to create a real-life simulation through a world-first virtual stope, recreating situations where miners encounter real time blast walls.
Motion capture technology originated in the life science market for gait analysis but is also used by visual effects (VFX) studios, sports therapists, neuroscientists, and for validation and control of computer vision and robotics.
SESSIONS TAILORED TO MINERS ARE A LIFELIKE “GAME” FOR TRAINEES THAT NEED TO ADAPT TO THE HARSH CONDITIONS OF MINE BLASTING
Anglo engaged Pretoria-based STS3D, a company specializing in safety training solutions for the mining industry, and STS3D partnered with Vicon, a motion capture developer with offices in the US and UK to create virtual reality (VR) training experiences.
Sessions tailored to miners are a lifelike “game” for trainees that need to adapt to the harsh conditions of mine blasting.
Tim Massey, Vicon product manager, said the use of the technology has great potential in mining, and a key differentiator is that trainees learn from mistakes made during gaming.
“You can be in a different scenario just by changing the setting. [It] has an emotional impact – which is hugely relevant in building an effective training experience. It has a huge impact on learning,” Massey told MINING.COM.
Johan Bouwer, head of new product development at STS3D, said the team aimed to apply the idea of video gameplay to mine safety training.
“Animation play made it easy to create. With the revitalization of VR, [it] became cost-effective for the enterprise community,” Bouwer said.
Bouwer said training centers are built around the need to train miners how to block off a blast wall, and drill on red dots, and tight timing sequencing was an issue.
“The problem was people were not marking properly. If you can get your blast correct – the value saves money,” Bouwer said.
Vicon and STS3D developed the VR wall, and used basic tracking technology to simulate painting on the wall – they have planted six VR walls for training in South Africa.
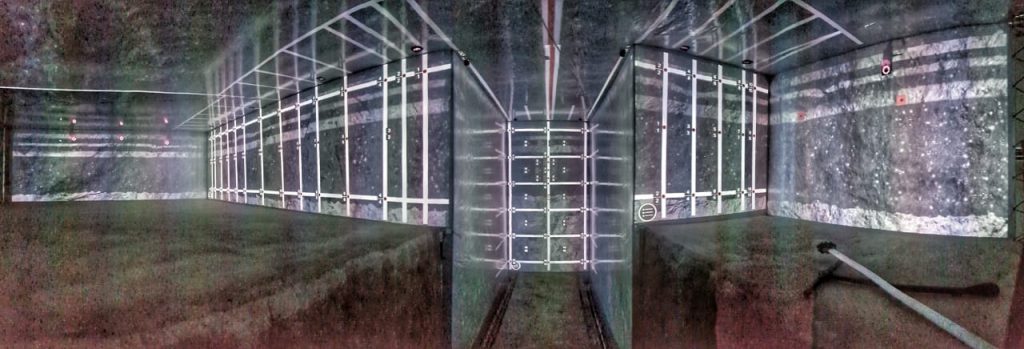
“Anglo needed a VR stope – the problem was we needed to tag direction, centre lines, and that has to be precisely accurate,” Bouwer said.
This technology, when used in the VR stope creates an experience that is visceral, and when tests go wrong – there is a virtual blast, complete with sound effects, and within the frame of the VR game, the trainee experiences a ‘virtual death’, which Bouwer said, “you can’t possibly forget.”
“This gives the miners a real fright. They’ll remember their error. Since you are fully immersed in the virtual mine, there’s no room for distraction. You’re on high alert all the time while marking a pattern on the rock face for the drill operators. And when you detonate the blast, the rock flies – creating a very vivid, a very memorable experience,” said Bouwer.
When a trainee makes a ‘fatal’ mistake – the rules of the game are that the miner has to start over.
Bouwer said he believes this approach can revolutionize how people are trained in mines, and can have the greatest impact where miners aren’t fully literate, as there is no need to read training manuals.
“It’s ‘serious games’ – you get so engrossed in the game you forget virtual reality and the audience watching – you get so engrossed in the program it becomes reality,” Bouwer said_Mining.com